Shape memory alloys are metals that, after being deformed by an external force, return to their original shape at a certain temperature. These metals are mainly alloys of titanium and nickel, and are used in various industries such as firefighting suits, eyeglass frames, and medical devices due to their resilience and light weight.
Shape memory alloys have been the subject of many interesting movies, most notably the Terminator series. In Terminator 2, the enemy T-1000 is a machine made of liquid metal that has the ability to change shape and self-heal. While the metal in the movie is described as “liquid metal,” it’s actually a technology still under research. However, the imagination of this futuristic technology is what gets us excited about the development of smart materials like shape memory alloys.
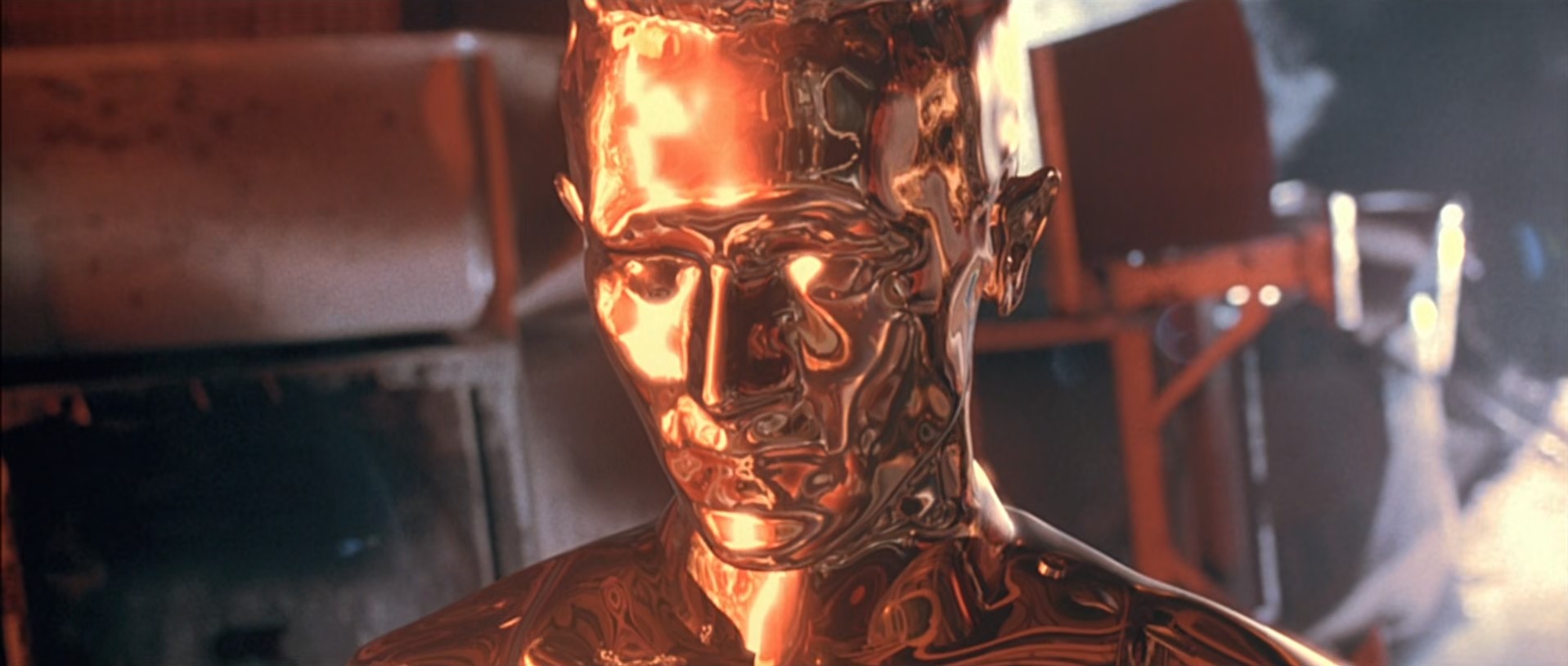
In general, metals have an inherent elasticity, which means that within their limits, they can be deformed by an external force and return to their original shape when the force is removed. This deformation is called ‘elastic deformation’. However, if a force is applied that exceeds the elastic limit, the metal will not return to its original shape and will be permanently deformed. This is called ‘plastic deformation’. When machining metals, it is possible to use this plastic deformation to shape the metal into a desired shape. For example, elongating and lengthening metal, hammering it, and thinning it out are all operations that utilize the principle of plastic deformation. However, there is an innovative material that goes beyond these traditional metals: shape memory alloys.
As the name suggests, shape memory alloys are metals that “remember” a specific shape. They have the ability to return to their memorized shape at certain temperatures. For example, if you bend a straight shape memory alloy bar into a coil and then place it in hot water, it will straighten back out as if it had remembered its original shape. Thanks to these properties, shape memory alloys are gaining traction in a variety of industries.
The way shape memory alloys work is due to their unique phase transformation. They are allotropes with two phases: at high temperatures, they remain in the austenitic phase, and as they cool, they change to the martensitic phase. During this process, the atoms in the metal move in a regular pattern that allows them to undergo a phase transformation very quickly, which gives them the ability to return to their original shape. In particular, alloys composed of titanium and nickel are the most typical shape memory alloys, and alloys made by mixing these two metals in a 50:50 ratio have new properties that go beyond the properties of the individual metals.
One of the most important characteristics of shape memory alloys is their resilience, the ability to return to their original shape at a certain temperature after being deformed by external forces. How can this resilience be utilized in real life? One example is firefighting suits. A molten iron made of shape-memory alloy is attached to the fire suit in a contracted state at room temperature, but when exposed to high temperatures, such as at a fire scene, the molten iron expands and forms an air layer inside the suit. This air layer creates a thermal barrier that helps protect the firefighters. Similarly, in cold environments, molten iron can expand to help retain heat inside.
A common example of shape memory alloys that we see every day are eyeglass frames. When eyeglass frames are bent or deformed, glasses made of shape memory alloy can be heated to restore their original shape. As you can see, shape memory alloys have practical applications in a variety of fields.
The first practical use of shape memory alloys began in 1963, when the National Aeronautics and Space Administration (NASA) created an antenna for the lunar surface. Since then, shape memory alloys have become increasingly popular in a wide range of applications, including mechanical parts, medical devices, underwear, clothing, and vehicles. For example, in the medical field, stents made from shape memory alloys are used to dilate blood vessels and aid in surgical procedures. In particular, shape memory alloys have also become popular in the aerospace and fashion industries, which require ultra-lightweight products due to their resilience and lightweight titanium as the main raw material.
However, several technical challenges remain in the development and commercialization of shape memory alloys. For example, nickel-titanium alloys have excellent properties, but they are difficult to machine and weld. To address this, new shape memory alloys with similar properties to nickel-titanium alloys are being actively researched to reduce production costs by using low-cost raw materials such as copper, zinc, and aluminum. If these developments continue, shape memory alloys are expected to be used in a wider range of industries in the future.