In chemical reactions, catalysts play an important role in speeding up reactions and maximizing efficiency by lowering the activation energy. Solid catalysts, in particular, optimize reaction conditions through components such as active ingredients, supports, and enhancers, which contribute to increasing the selectivity and performance of certain chemical reactions.
The minimum kinetic energy required for molecules to meet and proceed with a chemical reaction is called the activation energy. In a reaction with a small activation energy, the reaction proceeds quickly because there are many molecules with kinetic energy greater than the activation energy of the reaction. A substance that changes the rate of a reaction by controlling the activation energy is called a catalyst, and its ability to speed up a reaction is called catalytic activity. Catalysts provide new reaction pathways with different activation energies than those without catalysts. They play an important role in maximizing the efficiency of chemical reactions. The discovery and use of catalysts has led to important breakthroughs not only in the chemical industry but also in various scientific fields.
In the chemical industry, solid catalysts are often used because they do not require a separate process to separate the product, which can be liquid or gaseous, from the catalyst. These solid catalysts can be of various shapes and compositions, and customized catalysts are often developed according to the characteristics of the industry. For example, solid catalysts with different properties are used in petroleum refining, environmental remediation, and synthetic chemistry. These catalysts serve to increase efficiency and selectivity, which not only provides economic benefits but also has a positive impact on the environment. Solid catalysts are mostly composed of an active ingredient, a support, and an enhancer.
The active ingredient is the material that provides catalytic activity by adsorbing reactants onto its surface. In the catalysis of solid catalysts, the reactants are first chemisorbed onto the surface of the active component, the adsorbed reactants react on the surface and convert into products, and the products are then desorbed from the surface to complete the reaction. Metals are used as active ingredients in many reactions because a variety of substances can be adsorbed onto their surface. For example, iron is used as an active ingredient in the synthesis of ammonia, where the reactants hydrogen and nitrogen are adsorbed onto the surface of the iron and separated into their respective atomic states. The adsorbed reactants are stabilized by sharing electrons with atoms on the metal surface. The adsorption strength of the reactants depends on the type of metal. The adsorption strength must be appropriate. Weak adsorption results in low catalytic activity because the amount adsorbed is small, while too strong adsorption results in low catalytic activity because the adsorbed reactants are overly stabilized, slowing down the reaction on the surface. In general, in solid catalysts, the more active component atoms on the surface involved in the reaction, the more reactants are adsorbed, and the higher the catalytic activity.
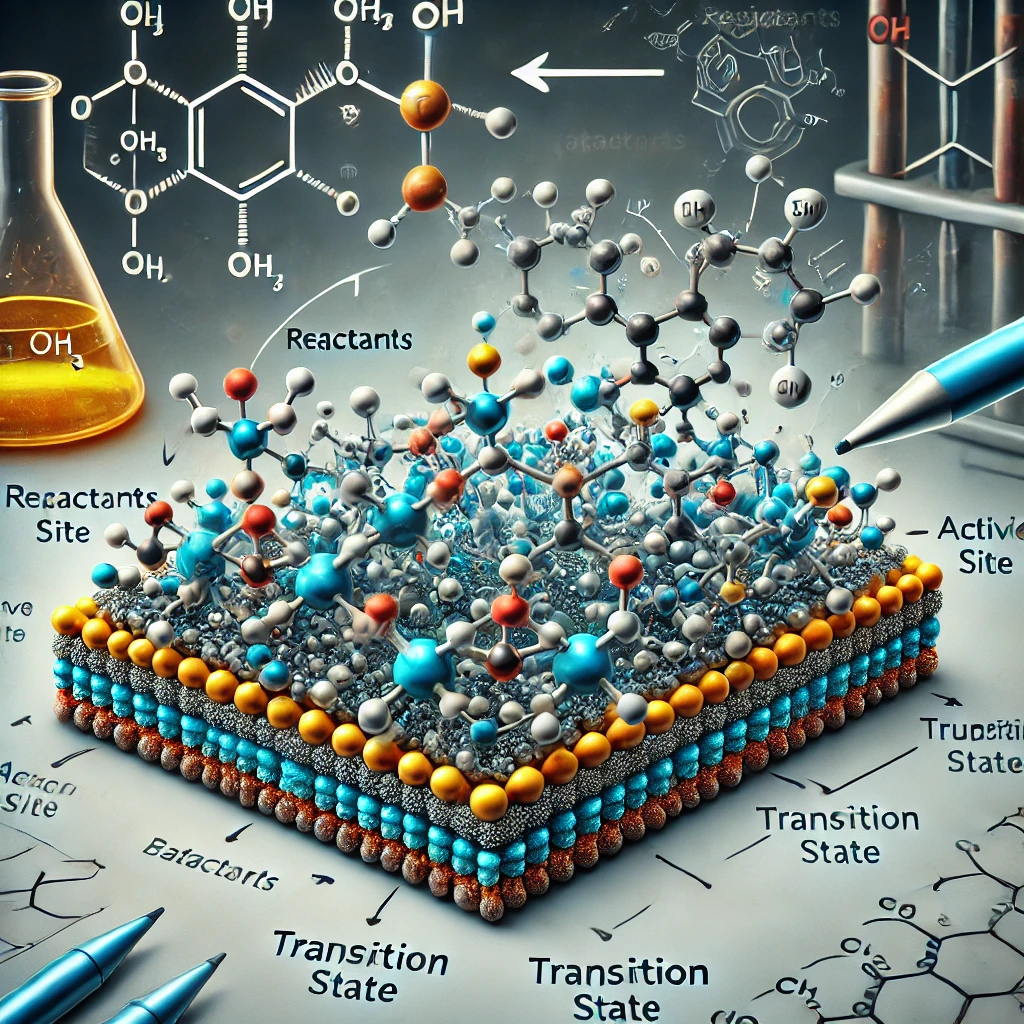
Metals have low thermal stability, so at high temperatures where chemical reactions occur, small particles made up of metal atoms stick together to form larger particles, which is called sintering. When the particles are sintered, the total surface area of the metal active ingredient is reduced. The solution to this problem is a support. When small metal particles are dispersed on the surface of a support with a large surface area and high thermal stability, the degradation of catalytic activity due to sintering is inhibited. Thus, even small amounts of metal can increase the activity of solid catalysts that use metal as an active ingredient. Support materials include alumina, silica, and zeolites, each of which offers properties optimized for specific reactions.
Enhancers are incorporated into the catalyst in small amounts to modulate activity. They can change the surface structure of the active ingredient to inhibit sintering, or they can change the electron density of the active ingredient to control the strength of adsorption. Solid catalysts must have an active component, but in some cases they do not contain any enhancers or supports. This varies depending on the application and required properties of the catalyst. For example, in catalysts used to purify exhaust from automobiles, precious metals such as palladium, platinum, and rhodium are used as active ingredients, and these catalysts are highly durable and efficient.
Furthermore, catalyst research and development is constantly evolving, with new materials and nanotechnology being used to develop more efficient and sustainable catalysts. This can contribute significantly to environmentally friendly processes and energy savings, and is expanding their application possibilities in various fields beyond the chemical industry. For example, catalysts using nanoparticles exhibit higher activity than traditional catalysts due to their high surface area and unique electronic properties. These advances will play an important role in making future chemical reaction processes more efficient and environmentally friendly. In the future, advances in catalyst technology are expected to open up new chemical reaction pathways and revolutionize various industries.